The advanced pre-combustion CO2 removal is effectuated by the Sorption Enhanced Water-Gas Shift (SEWGS) technology. This is a solid adsorption technology for CO2 capture from fuel gases in combination with water-gas shift and acid gas removal. The main objectives of the proposed STEPWISE project is to scale up the SEWGS technology for the CO2 capture from Blast Furnace Gas (BFG) with three overall demonstration goals in comparison to state-of-the-art technologies:
- Higher carbon capture rate
- Higher energy efficiency
- Better economy
The STEPWISE project achieves this by the construction and the operation of a SEWGS pilot test installation at a blast furnace site. This further reduced the risks associated with scaling up of technology. Additionally, adsorbent production scale-up and endurance testing are addressed. For the first time, three key components in the required technology chain are coupled together:
- an industrial Blast Furnace Gas source;
- subsequent BFG pre-processing using advanced water-gas shift technology;
- and finally CO and sulphur component cleanup with simultaneous CO2 removal in the SEWGS.
The consortium that achieved these goals represents 9 partners from 5 member states, bringing together technology providers, adsorbent and catalyst manufacturers, to system design and engineering companies through to an industrial end user, all committed to proactive dissemination and information exchange with stakeholders and other CCS technology developments.
The demonstration at a 14 t/d CO2 removal rate is used to prove the technology using real BFG. The performance is used to update the techno-economic evaluation and to assess the environmental impact relative to other state-of-the-art CO2 removal technologies. Moreover, it serves as basis for the design of a full-scale unit and associated costing. In parallel, alternative applications of the H2-rich SEWGS product gas within the steel plant configuration is investigated.
Technology Description
The heart of the advanced CO2 removal technology demonstrated in the STEPWISE project is the Sorption Enhanced Water Gas Shift technology, or SEWGS (see illustrative video). The SEWGS process was initially developed as a pre-combustion decarbonisation technology, and has the potential to reduce CO2 capture costs versus conventional removal processes such as solvent based systems. The process combines three processes in one reactor system:
- CO2 adsorption
- simultaneous acid gas removal (H2S, COS)
- the water-gas shift (WGS) reaction
Conventional approaches adopted for CO2 capture can require at least two water-gas shift reactors with interstage cooling to effect a high conversion of CO to CO2. Downstream the water-gas shift section, further cooling is then necessary to enable the capture of CO2 by absorption with a physical solvent. For a power application, the H2-rich gas again requires heating prior to feeding in a combined cycle.
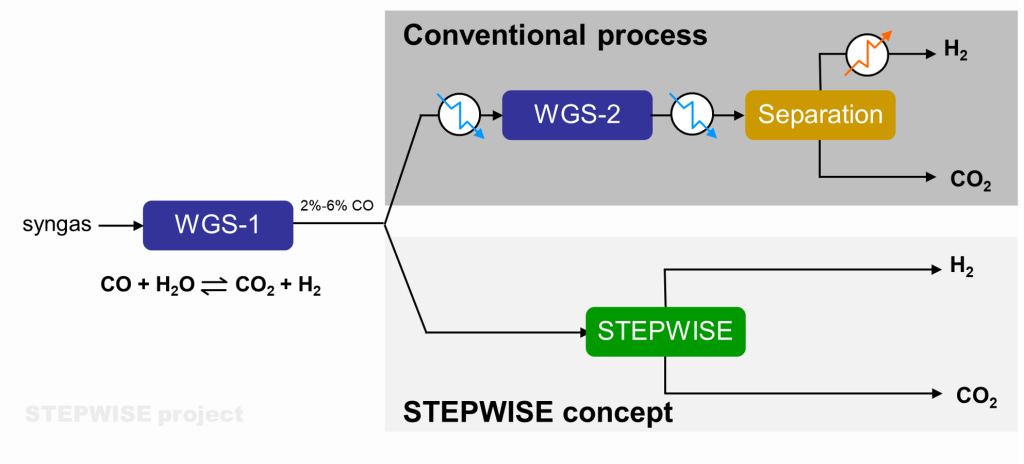
Using the SEWGS process, both the 2nd WGS reactor section and the H2/CO2 separation unit are replaced. Partially shifted fuel gas from the 1st WGS reactor is fed to the SEWGS unit, and a hot, high pressure, H2-rich product stream is directly produced. This H2-rich product at 400°C can be directly fed to the gas turbine or used in other applications at the steel mill. This removes the inefficiency of inherent temperature swings that is an essential characteristic of the conventional process. In addition, the SEWGS technology can yield a CO2 by product stream at sufficient purity for storage.
The SEWGS process is based on the unique characteristics of the K-promoted Hydrotalcite based adsorbent material. This material converts CO and adsorbs CO2 and other acid components such as H2S at elevated temperature and pressure. This produces a H2-rich product stream at temperature and pressure. Once the sorbent column nears saturation, the column’s pressure is released, and the sorbent material is regenerated using steam, producing a CO2 rich product. For a continuous process, multiple columns are needed, each in a separate step of the pressure-swing cycle. Apart from conventional PSA, this hot PSA operation allows using steam to drive the CO2-H2 separation. SEWGS is therefore special in that it can produce separate H2– and CO2-rich streams at high recovery for both components.